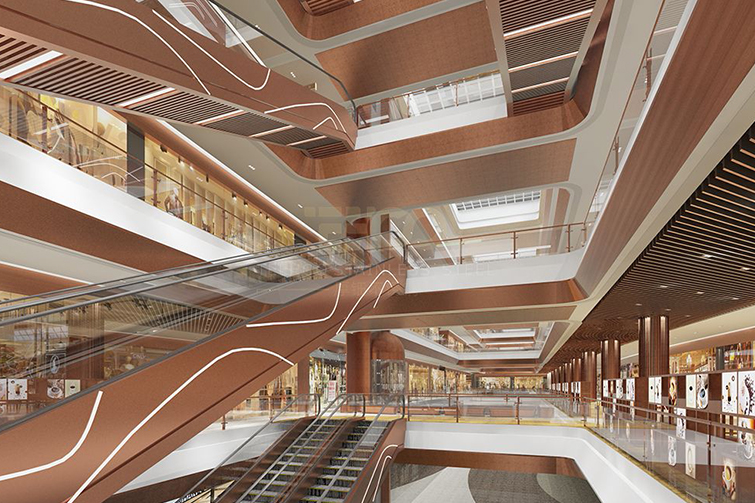
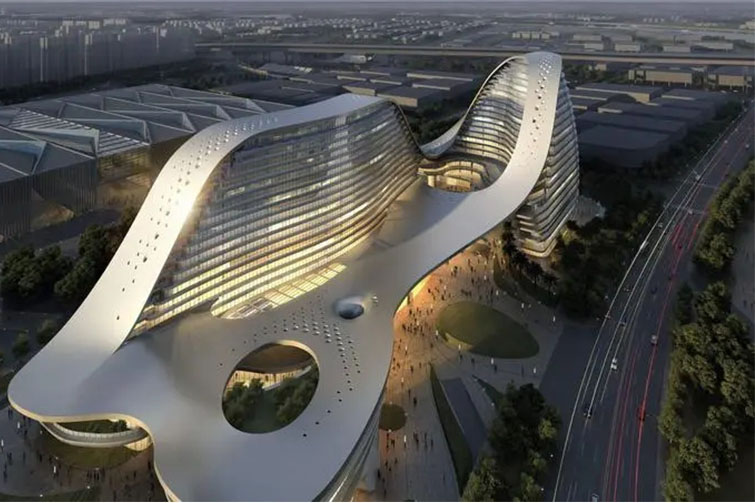
Understanding the New Standards for Stainless Steel: What You Need to Know
Stainless steel is a cornerstone material in many industries due to its durability, corrosion resistance, and aesthetic appeal. As the applications of stainless steel continue to expand, maintaining high quality and safety standards becomes increasingly crucial. Recently, new standards for stainless steel have been introduced to address emerging requirements and improve the performance and sustainability of this versatile material. This article explores these new standards, their significance, and their impact on various sectors.
1. Overview of Stainless Steel Standards
Stainless steel standards are established to ensure consistency in material properties, production processes, and quality control across the industry. These standards cover aspects such as:
- Chemical Composition: Defines the allowable percentages of various elements (e.g., chromium, nickel, carbon) that make up the stainless steel alloy.
- Mechanical Properties: Specifies the material's strength, ductility, and hardness, ensuring it meets the required performance criteria for its intended use.
- Corrosion Resistance: Sets parameters for the material's ability to resist degradation in different environments.
- Manufacturing Processes: Provides guidelines for the production, forming, and finishing processes to maintain uniform quality.
2. Introduction to the New Standards
The new standards for stainless steel have been introduced to address advancements in technology, evolving industry needs, and sustainability goals. Some of the key updates include:
Enhanced Corrosion Resistance: New formulations and treatment processes to improve the material’s resistance to various types of corrosion, including pitting, crevice, and stress corrosion cracking. This is particularly important for applications in harsh environments such as marine or chemical processing.
Higher Performance Grades: Introduction of new stainless steel grades that offer superior mechanical properties, including higher strength and better fatigue resistance. These new grades are designed to meet the demands of advanced applications in aerospace, automotive, and construction.
Sustainability and Recycling: Emphasis on the use of recycled materials and environmentally friendly production processes. New standards promote the adoption of sustainable practices throughout the stainless steel lifecycle, from raw material sourcing to end-of-life recycling.
Advanced Testing and Certification: Implementation of more rigorous testing methods and certification procedures to ensure compliance with the updated standards. This includes non-destructive testing techniques and more detailed quality assurance protocols.
3. Key New Standards in Stainless Steel
Several organizations set the benchmarks for stainless steel standards globally, including ASTM International, ISO (International Organization for Standardization), and EN (European Standards). Recent updates to these standards include:
ASTM A240/A240M: This standard specifies the requirements for chromium and chromium-nickel stainless steel plate, sheet, and strip for pressure vessels and general applications. The recent updates include new guidelines for alloy composition and mechanical properties to improve performance in demanding environments.
ISO 15510: This standard provides a unified specification for the chemical composition of stainless steels. The latest revisions include the addition of new grades with enhanced properties for high-temperature and high-corrosion applications.
EN 10088-1: This European standard specifies the technical delivery conditions for stainless steels, including bars, rods, wire, and profiles. Recent updates focus on the inclusion of new high-strength and corrosion-resistant grades, reflecting the latest technological advancements in metallurgy.
4. Impact of the New Standards on Various Industries
The updated stainless steel standards have significant implications for multiple industries:
Construction and Infrastructure: The introduction of higher strength and more corrosion-resistant stainless steel grades supports the development of more durable and long-lasting structures. This is crucial for projects in coastal areas or environments with high pollution levels where traditional materials may fail prematurely.
Automotive and Aerospace: The new standards facilitate the use of lightweight, high-strength stainless steels that contribute to fuel efficiency and performance in vehicles and aircraft. Improved fatigue resistance also enhances the safety and lifespan of critical components.
Medical and Food Processing: Enhanced corrosion resistance and the ability to withstand repeated sterilization cycles make the new stainless steel grades ideal for medical devices and food processing equipment. This ensures compliance with stringent hygiene and safety requirements.
Energy and Power Generation: For the energy sector, especially in oil and gas and renewable energy, the new standards provide materials that can endure extreme conditions and corrosive environments, thus ensuring reliability and reducing maintenance costs.
5. Sustainability and Environmental Benefits
The new standards place a strong emphasis on sustainability:
Recycling and Resource Efficiency: Modern standards encourage the use of recycled stainless steel, reducing the demand for virgin raw materials and minimizing the environmental impact of production. Stainless steel is inherently recyclable, and the updated standards promote efficient recycling processes to maximize resource use.
Lower Carbon Footprint: By improving energy efficiency in production processes and extending the lifespan of stainless steel products through enhanced performance, the new standards help reduce the overall carbon footprint of stainless steel production and usage.
Compliance with Environmental Regulations: The new standards align with global environmental regulations and initiatives aimed at reducing industrial pollution and promoting sustainable practices.
6. Challenges and Future Directions
While the new standards offer numerous benefits, they also present challenges:
Implementation Costs: Adapting to the new standards may require significant investment in new technologies, processes, and training. This can be a barrier for smaller manufacturers or those in regions with less developed infrastructure.
Global Harmonization: Ensuring consistent adoption and enforcement of these standards across different countries and regions can be challenging. Efforts towards global harmonization of standards are essential to facilitate international trade and ensure universal quality.
Continuous Innovation: As industries evolve and new applications emerge, stainless steel standards must continually adapt. Ongoing research and development are necessary to keep pace with technological advancements and changing market needs.
Conclusion
The new standards for stainless steel reflect the ongoing evolution of this critical material, responding to the demands for higher performance, sustainability, and broader application across various industries. By setting rigorous benchmarks for quality, corrosion resistance, mechanical properties, and environmental impact, these standards ensure that stainless steel remains a versatile and reliable choice for future innovation. As industries and technologies continue to advance, stainless steel will undoubtedly remain at the forefront, supported by standards that uphold its superior qualities and adaptability.